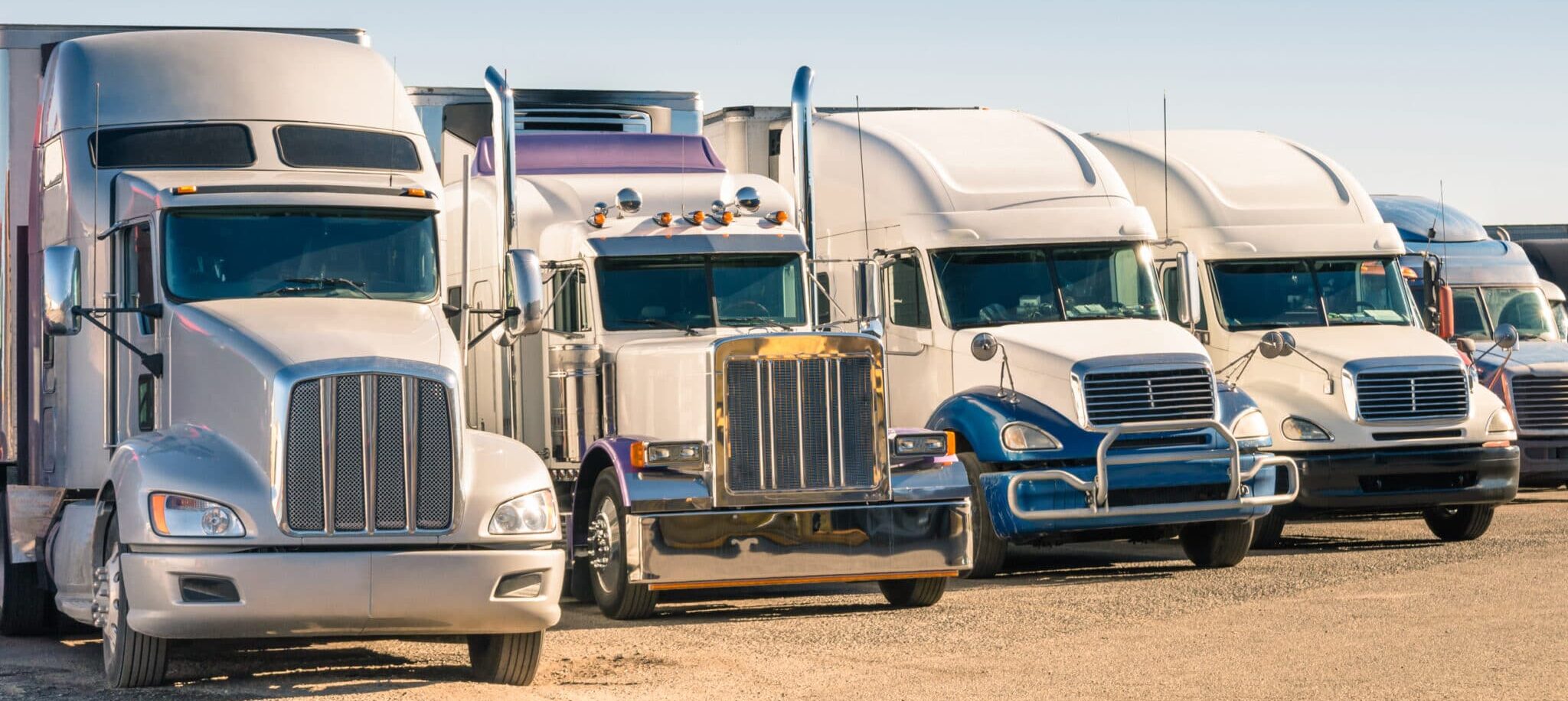
The Commercial Vehicle Safety Alliance (CVSA) has scheduled their Brake Safety Week for Aug. 22-28. During the week, commercial motor vehicle inspectors will conduct checks and remove commercial motor vehicles found to have brake-related out-of-service violations from the roadway.
In addition, inspectors will compile data on brake hoses/tubing, the focus area for this year’s Brake Safety Week, to submit to the Commercial Vehicle Safety Alliance (CVSA). CVSA will report its findings later this year.
Jurisdictions devote a week to conducting commercial motor vehicle inspections, identifying brake violations, and removing vehicles with out-of-service brake violations because:
-
-
- Brake system and brake adjustment violations accounted for more vehicle violations than any other vehicle violation category, accounting for 38.6% of all vehicle out-of-service conditions, during last year’s three-day International Roadcheck inspection and enforcement initiative.
- “Brake system” was the third most cited vehicle-related factor in fatal commercial motor vehicle and passenger vehicle crashes, according to the Federal Motor Carrier Safety Administration’s (FMCSA) latest “Large Truck and Bus Crash Facts” report.
- Brake-related violations accounted for eight out of the top 20 vehicle violations in 2020, according to FMCSA’s Motor Carrier Management Information System.
- During last year’s Brake Safety Week, 12% of the 43,565 commercial motor vehicles inspected were placed out of service for brake-related violations.
-
Why It Matters for CPG Shippers
In addition to out-of-service orders that take drivers off the road, many commercial operators choose not to drive during inspection weeks, which can have a drastic effect on capacity.
One of Zipline’s mid-sized East Coast and Midwest-based carrier partners reported that somewhere between 30-40 percent of their owner-operators choose not to drive during inspection events. These drivers frequently opt to forgo a week’s worth of work rather than face potential fines that result from a failed brake inspection or other various violations.
Regardless of the rationale, fewer trucks on the road means limited available options to haul your freight. This can translate into higher costs for customers booking orders. According to data collected at Zipline Logistics, rates were inflated by an average of 6 percent during inspection periods. This number can fluctuate further in markets where capacity is atypically strained.
Along with tighter capacity and higher rates customers can also expect to see:
-
-
- An increase in transit time for orders
- Possible service failures
-
How Zipline Can Help Get You Through Operation Safe Driver Week
Reach out to Zipline today to discuss the steps you need to take to adjust to strained trucking capacity. We can work with your organization to create scheduling, routing, or mode solutions for any foreseeable disruptions and keep your shipments on schedule.