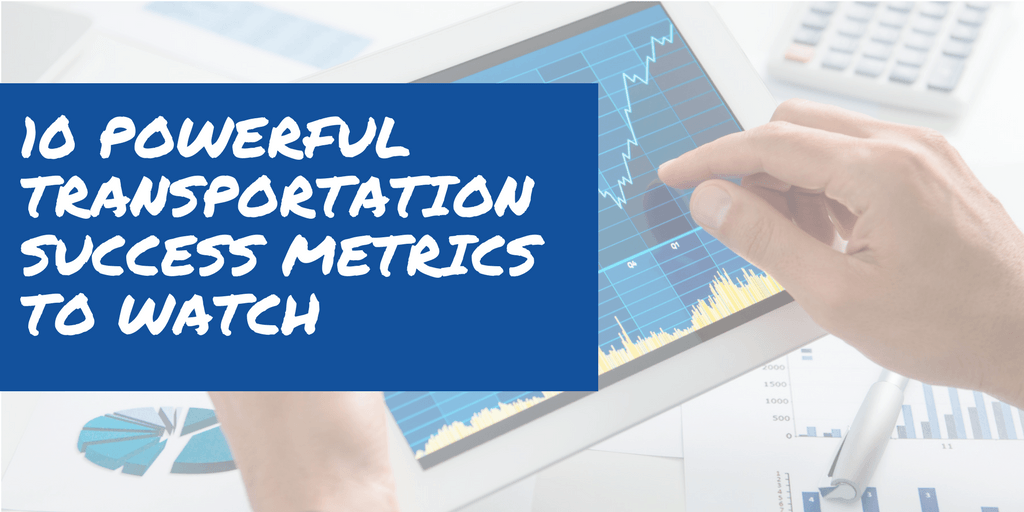
Management guru Peter Drucker famously stated, “If you can’t measure it, you can’t manage it.” Controlling the performance of business operations, which includes your supply chain and transportation, is nearly impossible without logistics metrics and data analytics.
These quantifiable measures and in-depth discoveries of useful information help evaluate the success of your organization in meeting your goals. In particular, the moving parts in your supply chain will be difficult to manage if you do not have a central dashboard that provides key performance indicators (KPI).
For example, smartphone supplier ZTE USA used metrics to deliver more items with an unchanged workforce by monitoring data analytics of their supply chain using supply chain software. In fact, they were able to grow their delivered volume by more than 70 percent in one year without adding more people. They credit much of their success to their supply chain’s data analytics; this information helped them ship more pallets without more people. They acknowledge that data analytics helped them plan, prepare, and communicate better to greatly increase their output with the same workforce.
Or look at Kraft Heinz. Their North American supply chain network includes 40 factories, 88 distribution centers, and more than 100 partners that help pack and manufacture their 7,000 SKUs. Plus, they are expanding their storage and warehouse facilities, making their landscape even more complex.
How can they monitor the pulse of this critical supply chain without analytics, key performance indicators, and dashboard metrics?
Smaller and medium-sized firms may function for a while without using metrics and data analytics. But to compete and scale upward and onward in today’s global marketplace, supply chain metrics are a necessary part of business.
The best advice: embrace metrics, measure your processes and operations, and take action to continuously improve them. This leads to smart decisions, better cost control, more revenue, and more profitability.
It’s best to start with knowing what’s important to measure and work within those objectives. Here are 10 logistics metrics that any firm, small, medium, or large, can and should embrace to measure the performance of their supply chain and transportation.
Top 10 Logistics KPIs and Logistics Metrics
1. Perfect Shipment Measurement
Sometimes called Perfect Order Measurement, you’ll find this KPI in most any discussion of supply chain metrics. It measures what percentage of your orders are without errors. In a way, it mimics the manufacturing concept of “zero defects” where the goal is to hone your manufacturing process by finding and eliminating defects incrementally until that number falls to zero. With perfect order measurement, you see and know what percentage of your orders are free of error and try to identify what’s causing any failures.
2. Freight Payment Accuracy
Measuring accessorial charges on freight bills allows a means of auditing the charges to identify any issues or erroneous billing errors or add-ons that could go unnoticed without attention. The metric puts focus on these charges and helps to pinpoint the recurrence of key incidences. Problems or issues may be monitored and resolved swiftly to avoid any unnecessary fees and charges and ultimately lower your transportation costs. A robust audit process can help save many dollars. The more error-free your freight bills and payments, the more you save, and the more net profit gravitates to your bottom line.
3. On-Time Delivery Adherence
Often also referred to as Must-Arrive-By-Date (MABD) Adherence. This metric is basic but revealing. It shows your batting average for delivering on time against the date required by your customers. This is particularly important for retail vendors to monitor, as they can lose margin if a carrier does not deliver merchandise on time. We’ve seen fees ranging from $50 to $5,000 for orders that show up late.
This metric may be expanded to indicate what percentage of items are delivered on time, the value of those that are, and how early or late they are. This, too, may be varied or broken down into smaller metrics. For example, the time from the warehouse to distribution center, or time from fulfillment center to customer shelf may all be measured separately or may be rolled into one longer-spanning metric. Any way it is measured, it allows you to see, monitor, and control so you can shape the most efficient supply chain.
4. On-Time Pickup Percentage
By monitoring the on-time pickup, shippers may see the timeliness of their carriers, and how it impacts delivery schedules. A measure of unacceptable pick-up times helps identify problems early on and makes it possible to avoid the carrier’s untimely behavior from impacting product delivery. It alerts supply chain leaders to take action and avoid customer dissatisfaction.
5. On-Time-In-Full (OTIF)
Somewhat of a combination of Perfect Order and On-Time, the OTIF metric measures the incidence of the customer getting what they want, when they want it. It’s a simple, but important measure of delivery. Many retailers score suppliers against this metric, as it helps indicate if the relationship is working effectively.
6. Out-of-Network Shipments
Out-of-network shipments originate from points that are less than optimal. If an order for product is normally fulfilled from inventory in a Chicago warehouse for delivery to a Michigan destination, but due to inventory depletion, it must be fulfilled from a warehouse in Philadelphia, then it is an out-of-network shipment. Monitoring such shipments and being aware of their patterns and trends help alert supply chain managers to an underlying problem. Because out-of-network shipments tend to be costly and inefficient, being able to study their pattern of occurrence allows shippers to better control, manage and resolve them. This metric helps identify inventory planning issues or shortcomings of others in the supply chain who may be contributing to the problem.
7. Average Cost Per Skid/Order
This metric incorporates all the apparent and hidden costs associated with the transportation and logistics cost, on average, per skid. This measurement will red flag high costs and allow an investigation to explain any upward spend. Action may then be promptly taken to remediate and resolve contributing factors.
8. Trailer Utilization Rate
This is the average utilization rate of a trailer asset. It factors in the average of used capacity. Ideally, 100% is most efficient. Measuring this indicates loading optimization concerns or problems and allows for better load planning. If shippers are underfilling trailers, they are overspending funds.
9. Average Dwell Time
This metric measures how long a carrier sits idle before being processed for pickup or delivery. Thus, it measures wait time. High dwell or wait times indicate an issue or concern that should be addressed. The problem could be dock congestion, production delays, understaffing, overbooking, inaccurate scheduling, etc. This is a particularly important metric now that carriers are subject to the ELD mandate. Sitting idle eats into their HOS and directly impacts profitability. Shippers with poorly functioning facilities and high dwell times will have difficulty attracting drivers and could be forced to pay more to secure capacity in today’s market.
10. Transit Time to Distance
For a given distance or lane, this measures the transit time to delivery. A higher transit time to distance may affect the attraction of drivers and carriers to transport such loads, given their ELD constraints and their intent to optimize their capacity.
—
Using methods to measure various aspects of your supply chain is key to a better and more efficient one. Embracing metrics and using them to drill down to the processes in your operations that need improvement is a smart practice that will result in better overall results.
Focus on your processes and find ways to improve them by using metrics; it is a smart business strategy that will benefit most any supply chain organization.
Metrics provide you the visibility to monitor your supply chain and change the process to move the needle in the right direction. Consultant and longstanding management thought leader Dr. W. Edwards Deming characterized this best when he stated, “Eighty-five percent of the reasons for failure are deficiencies in the systems and process rather than the employee. The role of management is to change the process rather than badgering individuals to do better.”
—
Logistics Spend Management: Savings Opportunities in the Supply Chain Looking to reduce your transportation spend? Check out our eBook for advice on how to identify untapped logistics savings opportunities. |